Building Sustainability into Control Systems > Air Handling Units
Introduction
Background
Control
Introduction
41 Cooper Square uses six air handling units (AHU) to heat, cool, humidify, and ventilate all indoor spaces. The Building Management System (BMS) utilizes an array of sensors to identify heating, cooling, and ventilation demands throughout the building. The BMS analyzes this data with a series of computational algorithms, and subsequently controls the building’s AHUs to maintain comfortable indoor conditions in an efficient manner.
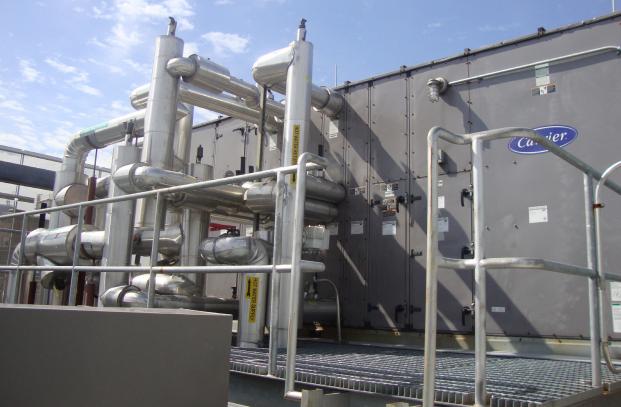
Air handling units are large heat exchangers, in which a flow of air is heated or cooled using water-filled heating and cooling coils. The air handling units draw air from outside the building using large centrifugal fans, and pass this flow through various smaller heat exchangers, filters, and humidifiers to supply air at the temperature and relative humidity specified by the BMS. Additionally, carbon-dioxide levels are monitored throughout the building in order to ensure that air-handling units are providing a sufficient flow of fresh air to keep indoor spaces safely ventilated. Figure 2 depicts one type of air-handling unit installed at 41 Cooper Square.
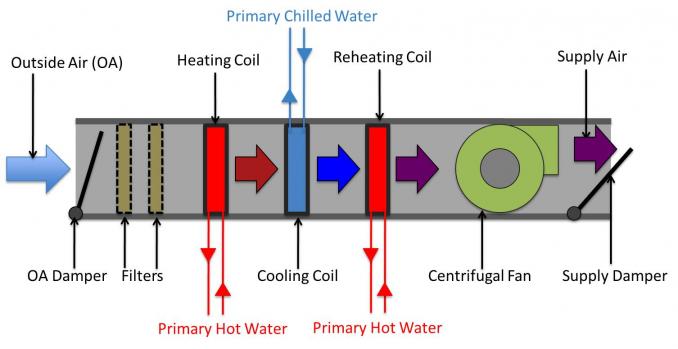
Figure 2 shows an AHU that treats a flow consisting of only outside air. Some other units in 41 Cooper Square are fitted with humidifiers or recirculation systems. This schematic, however, provides a good overview of the basic components of an AHU. First, the flow passes through a damper, which can be opened or closed to allow air to be taken into the unit. The air is subsequently filtered and passed through three radiator coils that heat, cool, and dehumidify the flow. It should be noted that these coils are filled with primary hot or chilled water from the boiler or chiller, respectively. The treated air, at the desired temperature and relative humidity, is subsequently passed through a centrifugal fan before it is directed to indoor spaces at the desired flow rate using supply dampers.
Background
Psychrometrics:
The study of the thermodynamic properties of humid air (a water vapor and air mixture) is known as psychrometrics. The humidity of air plays an important role in the comfort level of air. Air with a high humidity level is generally a problem during the summer. It limits the ability of a human to lose heat by the mechanism of sweating. It also can enhance the formation of mold. Air with a low humidity is generally a problem during winter, resulting in dry skin. Therefore, air taken into a building from outside must be conditioned. It must be cooled and dehumidified in summer, and warmed and humidified in winter. Psychrometrics allow engineers to define and quantify the state and energy content of a water vapor and dry atmospheric air mixture using seven distinct properties [1], listed below:
1. Dry Bulb Temperature: The Dry Bulb Temperature is the temperature of the air and water vapor mixture as measured by a simple thermometer. (Measured in Celsius or Fahrenheit)
2. Wet Bulb (or Saturation) Temperature: When discussing a mixture of water vapor and air, the Wet Bulb Temperature is the temperature that a volume of air would have if cooled adiabatically to saturation by the evaporation of water, all latent heat being supplied by the volume of air.This property is usually measured using a wet bulb thermometer or psychrometer (Measured in Celsius or Fahrenheit). It is always lower than the Dry Bulb Temperature (or equal for saturated inlet air streams).
3. Relative Humidity: A quantity used to describe the ability of a humid air stream to evaporate additional water vapor. It is the ratio of actual water vapor in the air to the maximum possible water vapor that the air could theoretically hold. Thermodynamically, this quantity is defined as the ratio of the partial pressure of water vapor in the air-water mixture to the saturated vapor pressure of water at the same conditions (pressure and temperature of the mixture). (Usually stated as a percentage)
4. Dew Point: The temperature at which the water vapor in humid air begins to condense if cooled at constant pressure. When air is at 100% relative humidity, it is saturated and at its dew point. Water vapor will begin to condense if it is cooled any further (Measured in Celsius or Fahrenheit). The lower the relative humidity, the lower the Dew Point.
5. Humidity Ratio: The Humidity Ratio is defined as the mass ratio of liquid water to dry air in a gas and vapor mixture. This quantity is usually expressed in pounds of moisture per pound of dry air. It is an important quantity in psychrometric calculations. The ability of air to “hold” water vapor (the vapor pressure) increases strongly with temperature. Therefore cold (winter) air can have a high relative humidity but a low absolute humidity. As cold air is heated, its absolute humidity stays constant, but the relative humidity decreases. Conversely, as hot (summer) air at a low relative humidity is cooled, its relative humidity increases. If the hot air is cooled below its dew point, the air becomes saturated and liquid water condensed, and this is a practical way to dehumidify air.
6. Specific Enthalpy: Enthalpy is a thermodynamic quantity equivalent to the total heat content of a substance, equal to the internal energy of the mixture plus the product of pressure and volume: h = u + pv. Specific enthalpy is the enthalpy of the humid per unit mass of dry air, and is usually expressed in Btu/lb of dry air or KJ/kg of dry air.
7. Specific Volume: The volume of an air and water vapor mixtusre that contains one unit mass of dry air. Usually expressed in cubic meters per kilogram of dry air, or cubic feet per pound of dry air.
These seven properties are graphically represented on psychometric chart, also known as Mollier Diagram, shown below in English units. The colored lines represent constant values of the corresponding property shown in the legend. Note, however, that the Dew Point line only exists where it is depicted in blue, coinciding with the line of constant 100% Relative Humidity (RH). This blue curve is also known as the saturation line.
Using this chart, any two properties of humid air can be used to determine the other five thermodynamic properties listed above. A psychrometric chart allows HVAC engineers to completely define the state of a water vapor and dry air mixture on a single diagram. Using this chart, it is possible to determine which processes are necessary to treat outside air to a desired temperature and humidity content. For example, Figures 4 and 5 show the manner in which hot, humid summer air is treated to comfortable set points.
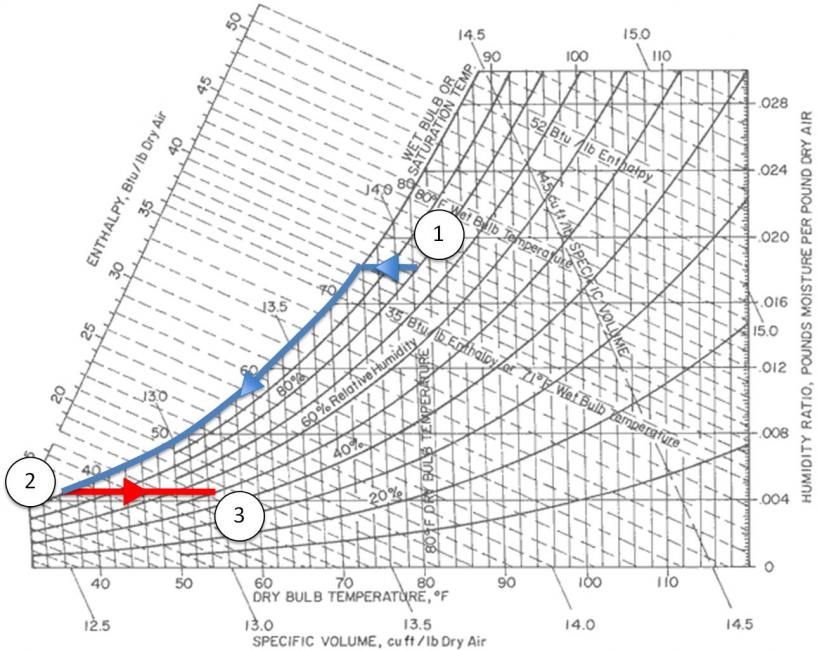
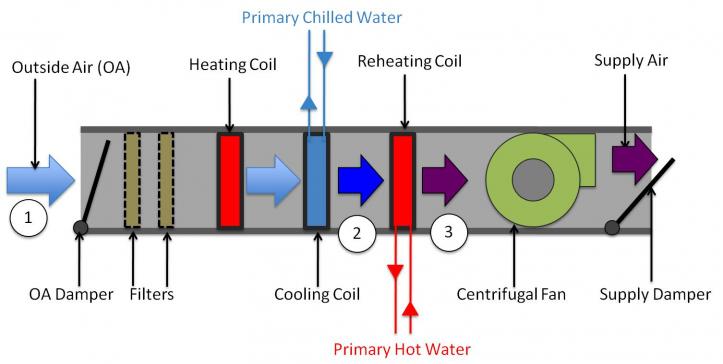
The outside air starts at a dry bulb temperature of 80 °F and 80% relative humidity, depicted as state 1 in the figures above. After passing through various filters, the flow is cooled by the cooling coils to the dew point temperature. As it cools further, water condenses out of the mixture, effectively dehumidifying the air until it reaches state 2. At this point, the flow is passed through a reheating coil that brings the temperature of the flow up to the nominal AHU supply set point of 55 °F, while decreasing the humidity level to 60% [3]. Note, the first heating coil is not utilized in this process. This heating coil is primarily used to heat outside air during the winter months.
AHU Design
41 Cooper Square uses six air handling units to provide treated air to classroom, office, auditorium and laboratory spaces. There are two main design differences between the six AHUs in 41 Cooper Square. First, AHUs can either be fitted with a humidifier or reheating coil. Second, the AHUs can either utilize 100% outside air or be fitted with a recirculation system. The application and principle of operation of these different designs are briefly covered in the following two sections [4].
Humidifier vs. Reheat Coil
The Rose Auditorium and most of the classrooms and offices in 41 Cooper Square are fitted with a radiant heating and cooling system. When in cooling operation, it is possible for the surface of the copper tubing in the radiant panels to be below the dew point temperature of the indoor air, and consequently cause condensation. This condensate can drip down from the panels and potentially damage electronic equipment. Consequently, it is important to dehumidify the air that enters spaces fitted with radiant cooling system. To accomplish this, AHUs 2, 3, and 6 are fitted with reheating coils. The reheating coils allow humid air to be dehumidified as illustrated in the Background section. Figure 6 is a BMS screenshot of AH-3, which utilizes a reheat coil to provide treated air to classrooms and offices in the cellar and on the ground floor.
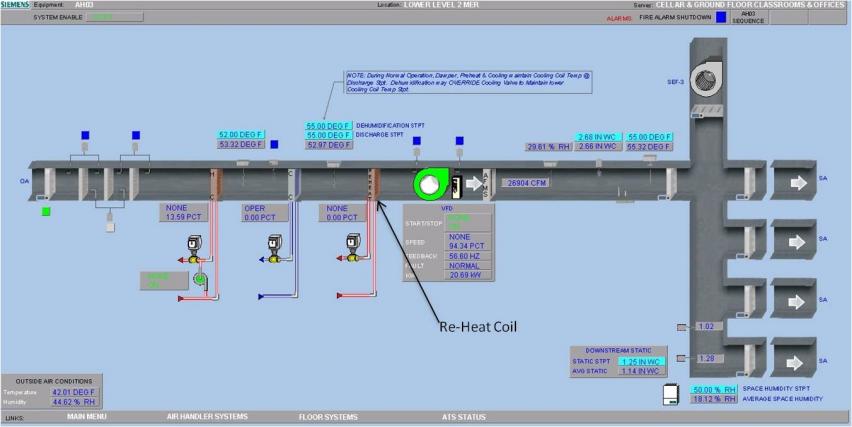
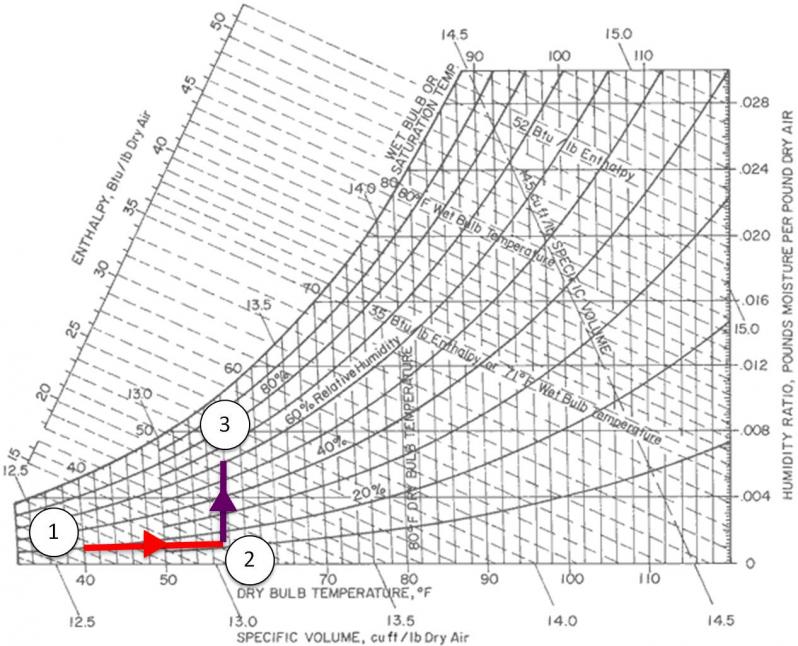
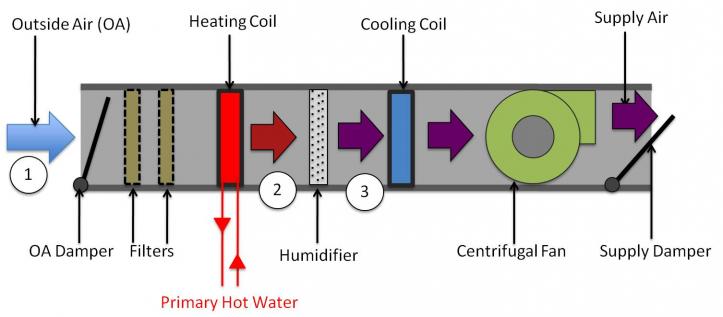
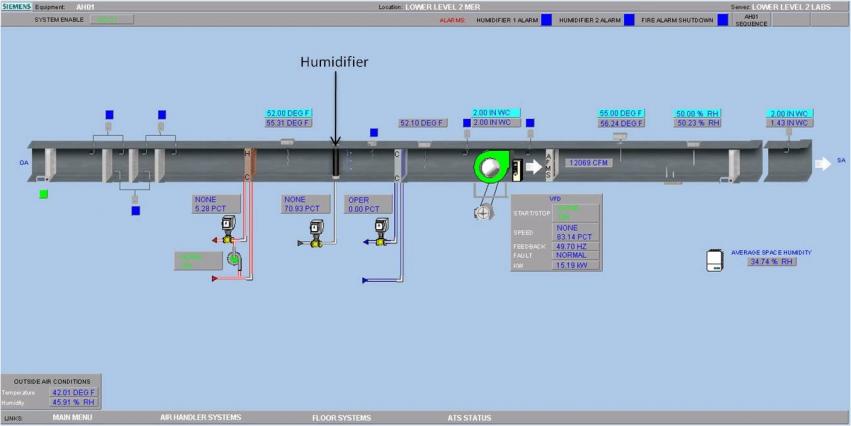
100% Outside Air vs. Recirculation System
Building codes require that all air which is circulated through laboratory spaces must be immediately exhausted outside the building in order to prevent potential contamination of the air supply system by harmful substances present in these laboratories. Using an air handling unit which treats 100% outside air to ventilate these spaces would be extremely wasteful and inefficient, as the energy invested into cooling or heating the air would only be utilized momentarily before being exhausted back outside. Consequently, 41 Cooper Square utilizes an innovative re-circulation system that allows treated air from non-laboratory spaces air to be recycled, and used to ventilate laboratory spaces before being exhausted.
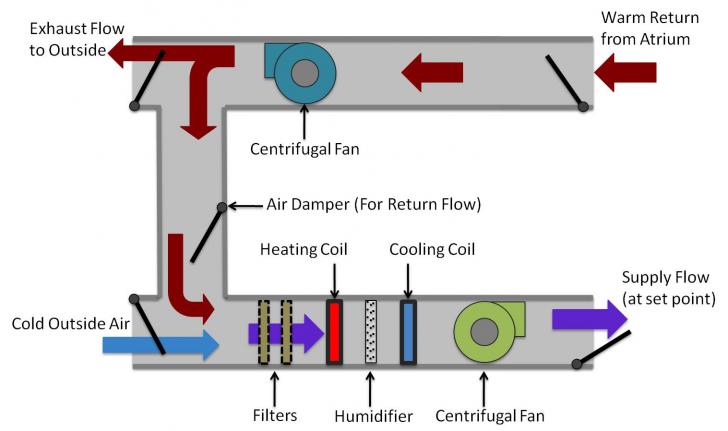
The schematic illustrates the manner in which the recirculation system can be used during the winter months to efficiently ventilate the building with warm air. The recirculation system draws warm indoor air from the top of the atrium using a large centrifugal fan. Some of this flow is exhausted outside the building, while the other portion is directed towards the air handling unit. At this point, the warm return flow is mixed with fresh, but cold, outside air and treated to the appropriate temperature and humidity set points. By mixing the warm return air with cold outside air, the AHU’s heating load and energy consumption are significantly reduced. Theoretically, it would be most efficient to treat only the return flow of air in a continuous loop. However, as air is passed through the building, it is contaminated with carbon dioxide from the occupants. Thus, it is always necessary to mix a certain amount of fresh air with the return flow in order to keep the building properly ventilated.
The flow rates of the outside air, return, exhaust and supply flows is modulated using variable air dampers. The BMS controls the position of these dampers (the degree to which they are opened or closed) by monitoring the flow rate, temperature, humidity, and carbon dioxide levels of the four flows with a large array of sensors. By analyzing the collected data, the BMS is able to calculate a ratio of return air and outside air that can be treated efficiently to meet the building’s ventilation demands, and subsequently output appropriate commands to the AHU’s dampers and other components. FIgure 11 is a BMS screenshot of AH-4, which ventilates laboratory spaces on levels 3 through 9 of 41 Cooper Square.
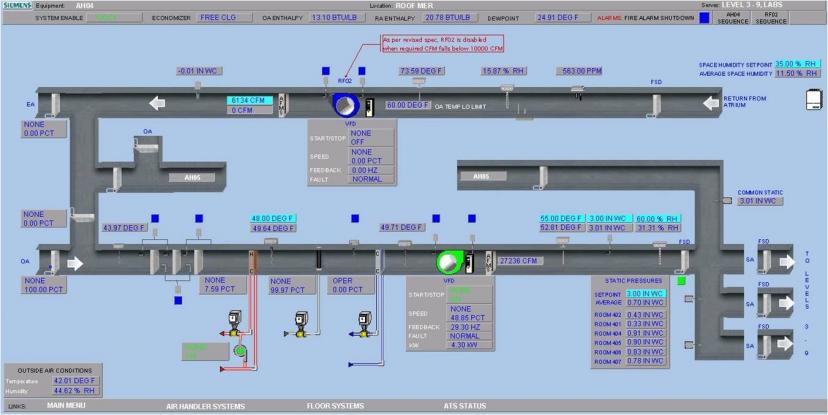
This BMS screenshot above shows the location of various sensors in the air handling unit. It should also be noted that this air handling unit is connected in parallel with AH-5, which also recirculates air from the atrium. A similar system is used in the Rose Auditorium, where significant energy savings can be achieved in treating the large space with a recirculation system.
AHUs with re-circulation systems have a greater upfront cost than those that use only 100% outside air. This increase in cost is largely due to the installation of the ducts and hardware necessary to collect and recirculate the return flow. 41 Cooper Square’s central atrium, however, allows the return flow to be conveniently collected at single point using natural ventilation. Thus, the building is able to efficiently treat small spaces with high occupancy rates, like classrooms and offices, with 100% outside air, and cheaply re-use this air to treat spaces with high ventilation demands, like the auditorium and laboratories.
Air Delivery: VAV Dampers and Reheat Coils
Once air is treated by the AHUs, it is sent through a channel of ducts to rooms throughout the building. Each room in 41 Cooper Square is fitted Variable Air Volume (VAV) dampers. These dampers control the flow of air into each room. Using these VAV dampers, the BMS is able to supply each room with the minimum amount of air required to maintain comfortable indoor conditions. For example, if an office is unoccupied, the VAV will only be opened slightly so that 40 CFM of air is allowed into the space, the minimum airflow required by New York Building codes. Reducing the airflow when unoccupied reduces the building’s overall energy consumption. Figure 12 is a BMS screenshot of an unoccupied office space illustrating the manner in which the VAV damper is used to control airflow into the room.
Some VAV dampers in the building, particularly those found in large spaces like classrooms and laboratories, are fitted with reheat coils that treat the flow of air prior to entering the room. These reheat coils allow the supply air temperature to be modulated according to the needs of individual spaces. Figure 13 is a BMS screenshot that shows a reheat coil fitted to the VAV damper in laboratory 407. In addition, the BMS laboratory 407 control panel illustrates the extensive fume hood exhaust systems that are installed in laboratory spaces to ensure that dangerous fumes can be safely ventilated out of the building.
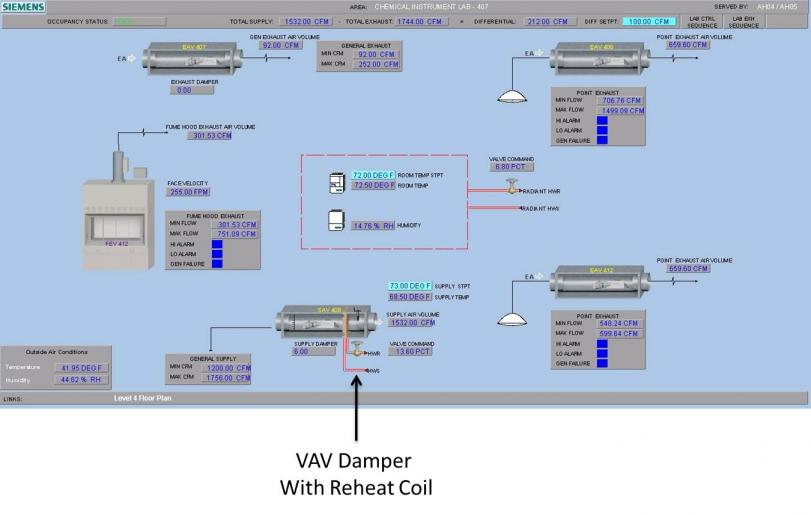
Control:
The BMS controls the operation of the AHUs to efficiently deliver air at the specified temperature and humidity. In addition, the BMS controls the flow of supply air to the various spaces to meet ventilation requirements. A brief overview of the various control sequences utilized by the BMS to operate these various air handling systems is provided in the following sections.
Control of AHU with 100% Outside Air:
The AHUs that treat 100% outside air consist of a single flow of treated air. Figure 14 is a BMS screenshot of AH-6 that highlights the various sensors and actuators used to monitor and control this type of AHU. First, the BMS opens the outside air (OA) damper to allow the unit to intake fresh outside air to be treated. This outside air is passed through various filters. In order to ensure that the filters are not clogged and functioning properly, the differential pressure (the difference between the air pressure before and after the filter) is measured using a differential pressure (DP) sensor. If the BMS detects a pressure drop exceeding a safe set point, an alarm is activated to notify technicians [3].
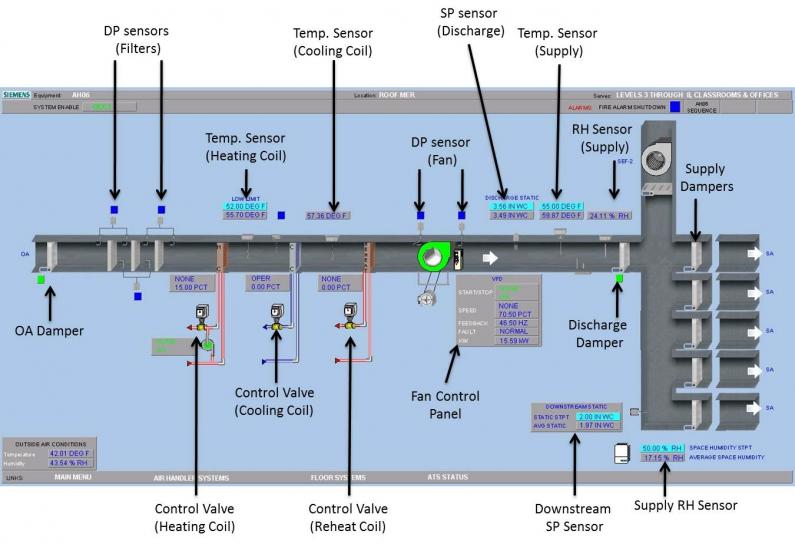
After filtration, the flow passes through various heating and cooling coils. The exact number and arrangement of these coils depends upon the type of room served by the AHU, as outlined in the Background section. However, after each heating or cooling coil, the temperature of the airflow is monitored by a resistance temperature detectors (RTD) temperature sensor. Using this temperature data, the BMS regulates the flow rate of primary water through the coils. For example, if the BMS detects that the airflow is too cold upon exiting the heating coil, the electronic valve actuator opens the valve allowing a greater primary hot water flow rate to enter the coil [3].
Treated air at the desired temperature and relative humidity is subsequently passed through a centrifugal fan. The AHU’s fan motor is controlled using a Variable Frequency Drive (VFD), which allows the BMS to modulate the operating speed and power consumption of the fan to meet ventilation demands. The BMS controls the fan’s operational speed as a function of the static pressure (SP) in the supply duct. When the supply SP is detected as falling below 2 inches of water column the fan speed is increased [3]. Conversely, when this SP set point in exceeded, the fan motor is ramped down to conserve energy. After exiting the fan, the temperature and humidity level of the flow are fed back to control the heating, cooling, and humidifying elements in the AHUs.
Control of AHUs with Re-Circulation:
There are additional sensors and actuators necessary to control the mixture of outside air and return air that is input to an air handling unit with re-circulation. Figure 15 is a BMS screenshot of AH-4, which depicts the various sensors and actuators used to control the re-circulation system.
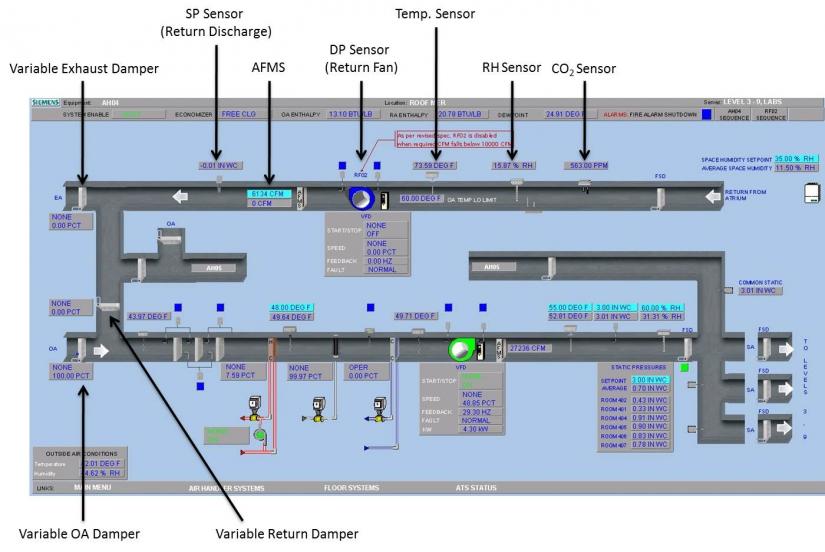
As described, the return airflow for AH-4 is collected at the top of the atrium. The temperature, relative humidity, and carbon dioxide content of this return flow are monitored using sensors in the return duct. The return flow is subsequently passed through a centrifugal fan. The fan’s speed is controlled by a VFD as a function of the static pressure at the discharge point.
After passing through the fan, the flow is either exhausted outside the building or re-directed towards the air-handling unit. The flow rate of air that is exhausted and re-circulated is controlled using variable air dampers, which are opened or closed by the BMS. The outside air damper in this type of unit is also variable, and the BMS is consequently able to control the exact ratio of fresh and return air that is treated by the AHU. This ratio is mainly controlled as a function of the carbon dioxide content in the return airflow.
The flow rate of air to the various spaces is controlled by the required ventilation in the various building spaces. Ventilation rates to indoor spaces are commonly quantified in terms of the number of times all the total volume of air in the space has been exhausted and replaced with treated air. For example, occupied laboratory spaces are programmed to receive between 10 and 12 air changes per hour. In order to conserve energy, this set point is lowered to 4 air changes per hour when the laboratory is unoccupied [5].
AHUs with re-circulation systems are also outfitted with a free cooling feature, which allows the unit to detect when conditions allow for maximum use of the re-circulation system to reduce energy consumption. As outlined in the Sequence of Operations, the AHU detects that the outside supply air (OSA) enthalpy is greater than the return air enthalpy, and closes the OSA damper to provide only the minimum amount of fresh air to meet ventilation demands. Thus, the AHU is able to conserve energy by utilizing return air that is already cooled below atmospheric conditions to lower the unit’s cooling load [3].
[1]Y. Çengel and M. Boles. Thermodynamics: an engineering approach, 7th ed. New York, McGraw-Hill, 2011
[2] "Psychrometric Chart Use (inner frame)." Homepages Web Server - UITS - University of Connecticut. N.p., n.d. Web. 20 Feb. 2012. http://www.sp.uconn.edu/~mdarre/NE127/NewFiles/psychrometric_inset.html
[3] G. Sampton. Sequence of Operation – The New Academic Building of Cooper Union. Morphosis Architects, Los Angeles, CA, Rep. 15959, June 2005. p. 4-6.
[4] GMP Set - The New Academic Building of Cooper Union – Modular Outdoor Air Handling Units. Syska Hennessy Group, New York, NY, 2007.
[5] Laboratory Ventilation Codes and Standards, Rev. 4, Siemens Building Technologies Inc., Munich, Germany, 2002, pp. 19.